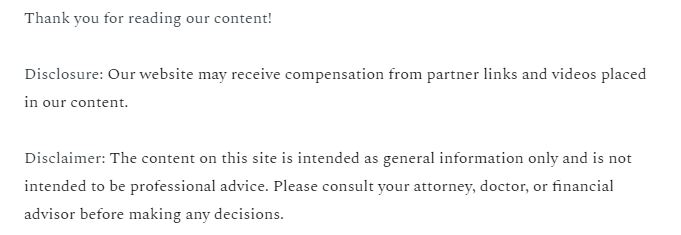

Air pressure is incredibly confusing and most people do not deal with it outside of filling up their vehicle’s tires with air. However, air compression and air compressor piping are pretty prevalent in most people’s lives. As a result, it is important to have a base understanding of what air compression is and how to to use it.
Approximately 70% of all manufacturers have a compressed air system. This compressed air can be used for a multitude of different functions. This is why air compressor piping is so commonplace across the country.
Compressed-air system leaks can be costly. So if you are suspecting that you are having issues with your air compressor piping, call an expert as soon as possible. Just one 1/8th of an inch hole in a 100 PSI system will cost nearly $1,200 a year in wasted energy. So getting any kind of leak is going to definitely save you some money on your air compressor piping
Energy audits conducted by the United States Department of Energy suggest that over 50% of compressed air systems at small to medium-sized industrial facilities have low-cost energy conservation opportunities. These energy conservation opportunities will save businesses huge money on their air compressor piping. So if you are able to utilize one of these opportunities you best get on it quickly!
Pressure loss in a properly designed system will be less than 10% of the compressor’s discharge pressure. This discharge pressure is something that can be found on a gauge on the outlet of the compressor. This is an important part of the air compressor piping system to keep an eye on!
If pressure loss is greater than 10%, evaluate your distribution system and identify areas causing excessive pressure drops. Every two pounds-per-square-inch decrease in compressor pressure will reduce your operating costs 1.5%. These drops in pressure will be harmful in both the long-run and the short-run as well.
Artificial demand is created when an end user is supplied air pressure higher than required for the application. If an application requires 50 PSI but is supplied 90 PSI, excess compressed air is used. Use pressure regulators at the end user to minimize artificial demand. All of these random facts on air compressor piping are why it may help to bring in an expert to help you out.
As much as 80 to 90% of the electrical energy used by an air compressor is converted to heat. A properly designed heat recovery unit can recover 50 to 90% of this heat for heating air or water. Approximately 50,000 British thermal units, also known as Btus, per hour is available per 100 CFM of compressor capacity when running at full load.
If your compressed air system does not have an air receiver tank, add one to buffer short-term demand changes and reduce on and off cycling of the compressor. The tank is sized to the power of the compressor. For example, a 50 hp air compressor needs approximately a 50-gallon air receiver tank. When intaking cooler air, which is denser, compressors use less energy to produce the required pressure. For example, if 90 degrees Fahrenheit intake air is tempered with cooler air from another source to 70 degrees Fahrenheit, the 20 degrees Fahrenheit temperature drop will lower operating costs by almost 3.8%.
In Conclusion
There are so many areas of life and work in which you will benefit from getting the help of a paid professional. Dealing with air compressor piping systems is definitely one of these areas. A talented and reliable expert can swoop right in and help you not only save money but even potentially get ahead of other problems that you may face.