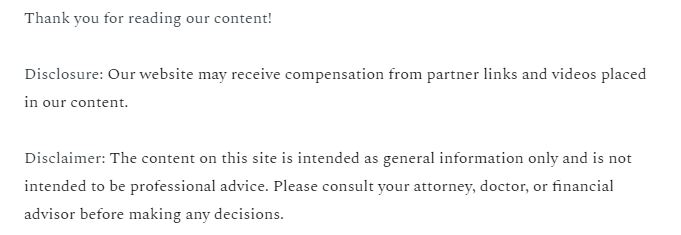
Used in approximately 70% of all manufacturers including for car detailing equipment, the compressed air piping design is a common system that is used in a number of industries. Although this is a highly useful and beneficial process, the compressed air piping design can also be very expensive to repair or to operate with imperfections. For example, a 1.8 inch diameter hole in a 100 psi system can cost as much as $1200 a year in energy that is wasted. For this reason, preventative maintenance is important. By keeping up with small repairs like fixing holes as soon as they are discovered, expensive repairs can avoid even more expensive problems further down the line.
The Most Efficient Compressed Air Piping Designs Help Businesses Save Money
The latest research indicates that 70% of all manufacturers have a compressed air system. From aeronautics engineers to car mechanics, the use of compressed air is an important part of many jobs. As another example, compressed air systems for heavy equipment allow the efficient operation of machines without the use of additional fuel. Consider some of these facts and figures about the important role that compressed air plays in a number of industries:
- 50% of compressed air systems at small to medium sized industrial facilities have low-cost energy conservation opportunities, according to energy audits conducted by the U.S. Department of Energy (DOE).
- 80% to 90% of the electrical energy used by an air compressor is converted to heat, so it should come as no surprise that a properly designed heat recovery unit can recover 50% to 90% of this for heating water or air.
- Registered on a gage found on the outlet of the compressor, pressure loss in a properly designed system will be less than 10% of the compressor’s discharge pressure.
- When intaking more dense cooler air compressors use less energy to produce the required pressure. For example, if 90 degree F intake air is tempered with cooler air from another source to 70 degree F, the 20 degree F drop will lower operating costs by as much as 3.8%.
- Adding an air receiver tank to a compressed air system does can buffer short-term demand changes and reduce the on and off cycling of the compressor. These receiver tanks are sized to the power of the compressor. For instance, a 50 hp air compressor needs approximately an air receiver tank that is 50 gallons in size.