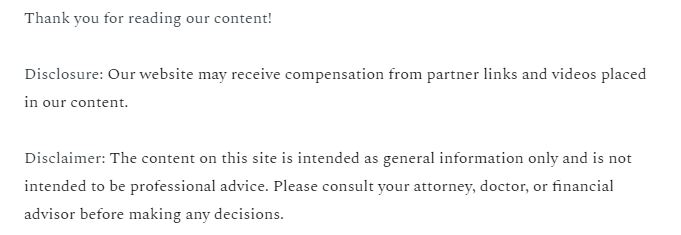

How familiar are you with modern compressed air piping design? Electricians and designers are hard at work every year improving air compressor pipes in residential and institutional buildings, creating cleaner air and more reliable circulation in light of mounting energy costs and environmental safety. Compressed air piping materials need to be heavily analyzed when installed or replaced in order to encourage the very best compressed air piping design and function.
How Common Are Air Compressors?
Air compressor pipes are constantly being improved and redesigned to catch up to modern standards. Did you know around 70% of all manufacturers have some form of compressed air system? These are one of the most common behind-the-scenes technologies, circulating electricity and clearing the air to create the most comfortable environment possible. While these can be expensive, they’ll be distinctively less so if you participate in routine maintenance.
How Expensive Are They?
Compressed-air system leaks are known to be incredibly costly. For example, an 1/8 inch diameter hole in a standard 100 PSI system can cost you more than $1,200 per year in wasted energy costs. Want to save money? Regularly double-check your system for potential maintenance and plug up any and all sizable leaks you see. Even a minor crack or leak can see your energy being wasted in real time.
How Can I Recover Energy?
If you want your compressed air piping design to maintain a proper balance between costs and energy disposal, you need to keep an eye on its inner workings. As much as 80% to 90% of the electrical energy used by air compressors is converted to heat, while a properly designed heat recovery unit can recover up to 90% of the heat for heating either air or water. Energy audits conducted by the U.S. Department of Energy (shortened to DOE) suggest at least 50% of compressed air systems at either small or medium sized industrial facilities have low-cost energy conservation measures.
How Is Energy Measured?
Around 50,000 British thermal units (shortened to Btus) per hour is available every 100 cfm of compressor capacity — however, this is only when it’s running full load. If the pressure loss is greater than 10%, you need to evaluate your distribution system and try to identify areas causing greater than average pressure drops. Even two pounds-per-square-inch decreases in compressor pressure can reduce your operating costs by nearly 2%.
What Makes Good Compressed Air Piping Design?
Whether it’s finding good air fittings or analyzing your compressed air piping sizing, compressed air piping design requires you be proactive, analytical and up-to-date on the latest technology. If your compressed air system doesn’t have an air receiver tank, try adding one to better buffer short-term demand changes — this will reduce on and off cycling of your compressor. After all, the tank is sized to the power of the compressor and a standard 50 HP air compressor will need a 50-gallon to compensate. Think your cushion clamps are up to snuff? It’s never been a better time to check.